GM To Partner With Autocar For Heavy Duty Work Vehicles
General Motors and Autocar Industries, LLC recently entered into a collaborative development agreement to craft a lineup of heavy duty work vehicles with zero tailpipe emissions. But, these “cutting-edge” vehicles will be propelled by GM’s innovative HYDROTEC hydrogen fuel cell systems. So, there are going to be some significant barriers to adoption.
Autocar, considered by GM to be a leading player in tailored medium and heavy duty work trucks, sees this initiative as a significant step forward in providing powerful, zero tailpipe emissions solutions to its customers. Fuel cell technology offers an added energy propulsion choice to support Autocar’s professional and industrial customers that can help them meet emissions and regulatory goals.
GM says hydrogen fuel cells are a key component of the company’s electrification strategy which extends beyond battery-powered passenger vehicles like the Bolt EV and EUV. For those unfamiliar, fuel cells combine hydrogen and oxygen to generate electricity through an electrochemical reaction. The fuel cell enables the conversion of energy stored in hydrogen into electricity to power a vehicle, while not producing tailpipe emissions other than water.
“EV propulsion systems like GM’s Ultium Platform are great solutions for electrifying passenger vehicles, but larger vehicles like Autocar’s class 8 trucks, refuse trucks and terminal tractors require robust solutions that enable significant energy carrying capacity and fast refueling times,” said Charlie Freese, GM executive director, Global HYDROTEC. “We want to enable zero tailpipe emissions solutions for the largest, highest energy consuming vehicles, and fuel cells are ideal for the most energy intensive applications.”
GM says HYDROTEC power cubes are compact, easy to package into an overall vehicle design, scalable, and can electrify vehicles and applications across a variety of industries, from freight trucking, aerospace and locomotives to power generation.
The Autocar Truck Plant in Birmingham, Alabama, is set to begin production of the first of these vehicles in 2026. Autocar will be responsible for building and customizing vehicles with HYDROTEC technology, which will then be directly sold to customers. The initial focus will be on manufacturing cement mixers, roll-off and dump trucks, all of which share a common architecture. Following this, garbage trucks and terminal tractors will be produced.
“Autocar provides customized vocational trucking solutions, and as regulations change, we see HYDROTEC fuel cells as an additional avenue for our customers to meet their EPA requirements with zero tailpipe emissions vehicles,” said Eric Schwartz, president, Autocar. “GM’s scale, reliability and the capability of their HYDROTEC fuel cell technology will enhance Autocar’s existing platforms.”
Each power cube is equipped with over 300 hydrogen fuel cells, as well as thermal and power management systems. It also incorporates proprietary controls to enhance fuel cell and battery performance, while optimizing cold start capability. With an output of 77 kilowatts, the HYDROTEC power cube offers significantly quieter operation compared to conventional diesel propulsion systems. For even higher power ratings, multiple power cubes can be conveniently arranged within a vehicle to provide the extra charging power needed.
Triz Engineering offers specialized integration support for power distribution between fuel cells and batteries. These batteries store electricity generated from regenerative braking or produced by HYDROTEC power cubes. Triz Engineering is a commercial vehicle engineering company that is part of the GVW Group, which also owns Autocar. Adding batteries into the mix allows for smaller or fewer hydrogen fuel cells while still being able to handle short duration peak loads on the EV system.
“We have carefully studied existing severe duty vocational trucks to understand their specific demands and requirements,” said Johann Vorster, president of TRIZ Engineering. “With GM and Autocar, we have built a fuel cell application that is unique within vocational vehicles — giving severe duty trucking more options to be truly rugged and capable of achieving zero tailpipe emissions.”
Upsides and Downsides
At the vehicle level, fuel cells are lightweight and enable large payloads, excellent range, quiet operation and rapid refueling, so they can meet the needs of the heaviest duty applications that batteries struggle with. But, they come with another significant challenge: hydrogen infrastructure. You can find electricity almost anywhere in the 21st century, but getting a hydrogen fueling station up and running is another matter. So, it isn’t the simple trade-off hydrogen proponents say it is.
On the other hand, the technology has a much higher energy density. Instead of hauling a large battery pack around that cuts into vehicle payload, hydrogen tanks can allow the heaviest trucks to be economically and regulatorily viable while battery technology improves. The technology is wasteful and inefficient for most small passenger vehicles, but it still has a place in heavy duty applications when infrastructure is available.
In the long run, the inefficiency of hydrogen production and the greenwashing potential is probably not going to be good for the technology’s future.
Efficiency wise, the problem comes from repeated conversion losses. It takes a lot of electricity to obtain the greenest hydrogen through electrolysis. Then, the hydrogen must be collected, compressed, pumped into storage, pumped into a tanker truck, transported, pumped into another storage tank, and then pumped into the vehicle where more energy losses occur. All in all, hydrogen vehicles use around 5-10x more energy per mile of range.
The other dirty secret is that hydrogen doesn’t all come from electrolysis. In fact, at present very little does. Most of it comes from existing fossil fuel processes, especially natural gas production. This gives fossil fuel companies to produce a “green” product that came from non-green sources. For that reason, hydrogen is a technology that must be carefully monitored for basically being a scam.
There may be industries, such as long-haul cargo planes, where hydrogen will remain a viable choice for many decades. But, for most short and medium range trucking operations, a battery system does a better job than hydrogen for a lot cheaper and with a lot less wasted energy. GM and its new partners may eventually find that companies decide that the cost of operation and the challenges of infrastructure make it kind of a dead end in most places.
But, there may be places and niche applications that end up surprising us. So, we’ll have to wait and see how this actually turns out for the company.
Featured image provided by GM.
Have a tip for CleanTechnica? Want to advertise? Want to suggest a guest for our CleanTech Talk podcast? Contact us here.
Latest CleanTechnica.TV Video
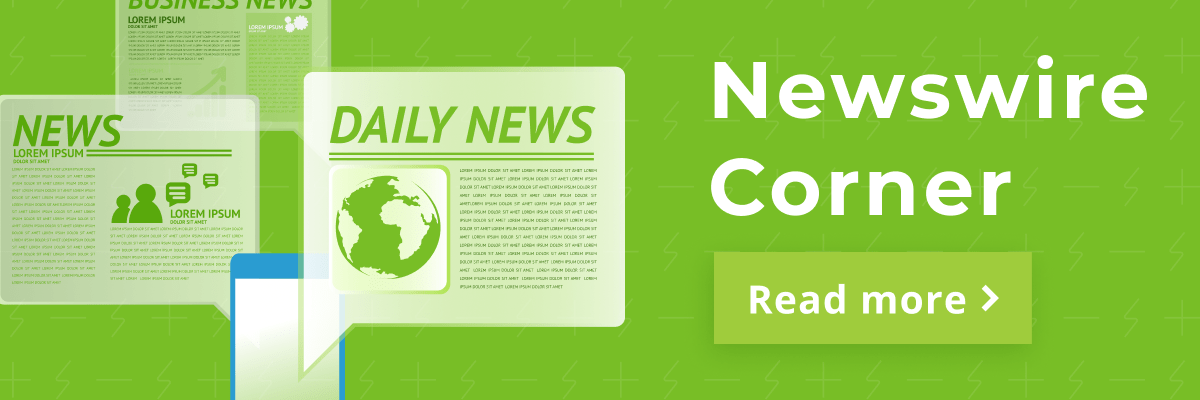
CleanTechnica uses affiliate links. See our policy here.